If you have an appreciation for Japanese art, then Katanas are likely to capture your interest. These Samurai swords, once exclusively wielded by the elite, continue to be crafted using the same ancient tradition that has been passed down over millennia.
Katana blades are renowned for their unmatched sharpness, strength, flexibility, and ease of use, qualities that surpass those of any other sword, even in the face of modern technology and forging techniques.
Today, there are only a few Japanese Katana swordsmiths remaining, each a master in their craft. The primary focus of this article is to offer you insights into the traditional methods of crafting Katanas and where you can find authentic pieces.
Making Katanas: The process
The crafting of Katanas involves a fascinating journey, beginning with the creation of tamahagane, the steel used for the sword. This steel is produced by smelting iron sand, which is sand containing iron ore, along with charcoal in a large clay furnace called a tatara.
Tatara masters meticulously oversee the process once the furnace reaches the correct temperature, adding iron sand and charcoal as needed. This stage requires continuous monitoring, with the team remaining on-site for 72 hours without interruption for the process to be successful.
Inspecting the steel
Once the three-day smelting process is finished, the tatara masters extract the tamahagane from the clay furnace. The steel mass is then separated based on its carbon content.
Blending high-carbon steel and low-carbon steel creates blades with razor-sharp edges and outstanding toughness. Swords made solely from one type of steel would either be brittle or prone to dulling quickly.
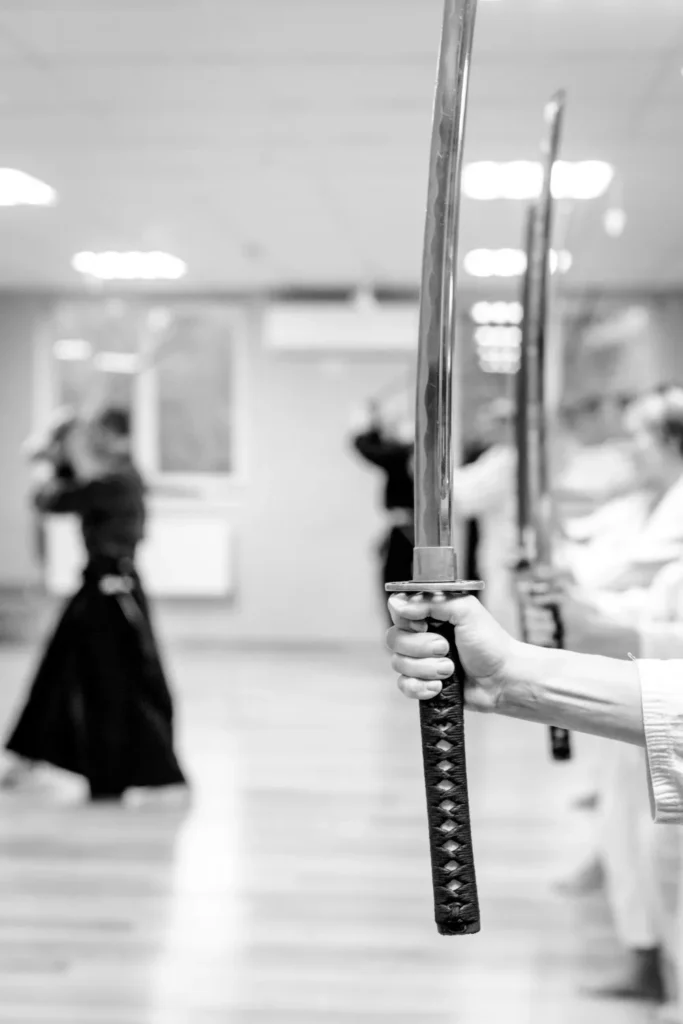
Removing impurities from steel
To enhance the bonding of iron and carbon in the tamahagane and remove any residual impurities like slag, the upper portions are sent to a swordsmith. The swordsmith then heats, hammers, and folds them repeatedly.
Blade smithing
In the third step, the smith heats high-carbon steel and forms it into a long piece with a U-shaped channel, ensuring impurities are removed through hammering. Additionally, a strip of low-carbon steel is hammered into a shape that fits precisely within the channel and is heated. Subsequently, the two metals are forged together. This process ensures that the two types of steel, high-carbon and low-carbon, are properly positioned; the high-carbon steel forms the sword’s outer shell, providing a sharp edge, while the low-carbon steel serves as its core.
Anodizing the blade
After assembling the blade steel, the next step involves a second firing. The upper sides and blunt back edges of the blades are coated with a thick mixture of clay and charcoal powder, with only their primary edges left barely covered.
When the blade is polished, this design, known as hamon, is revealed. It not only provides protection but also adds visual appeal to the blade. The blade is then heated to a temperature just below 815°C (1500°F). If the temperature exceeds this, the blade will crack.
Curving the blade
The blade is pulled from the fire and swiftly immersed in water, a process known as quenching. The varying contraction speeds and degrees of the two steel types used in the blade cause it to bend, resulting in the distinctive curve that is characteristic of a sword.
Blade polishing
Once the blade is fully forged, it is handed over to the sword polisher for meticulous polishing. This process involves using a series of grinding and polishing stones to achieve a razor-sharp edge on the sword. The polishing step can sometimes span months to complete.
Assembling the blade
Metalworkers attach the blade to the sword’s hilt, including its ornamental guard. Next, the blade is inserted into a lacquered wooden scabbard, which is intricately decorated by skilled artisans.
The handle is then crafted using materials like gold, leather, or stone. These final steps add artistic finishing touches that complement the blade’s craftsmanship.
This journey showcases the meticulous process a Katana undergoes before reaching the finishing phase, highlighting the craftsmanship involved.
How do you buy affordable and Excellent Quality Katanas?
From the outset, it’s clear that crafting a Katana is no ordinary feat. With the decline in the number of Katana makers, their exclusivity has surged, leading to escalating prices due to reduced competition.
While we acknowledge the dedication and skill evident in the craftsmanship of truekatana.com, from a collector’s standpoint, there are also affordable options available.
China, particularly Longquan, stands out as a hub for producing durable Katana swords. With a history spanning over 2600 years and renowned as a city of family swords, Longquan is among the world’s premier locations for sword manufacturing.